WHAT WE DO
RECLADDING
What is Recladding and why is recladding a legal requirement if required?
Recladding, the process of replacing a building’s external facade, involves creating a ventilated space between the original wall and the new facade. This design allows for improved airflow, effectively removing moisture from the building and enhancing its thermal performance.
With our profound knowledge of building exteriors and strategic partnerships within the supply chain, GSIM possesses extensive expertise in the re-cladding of structures.
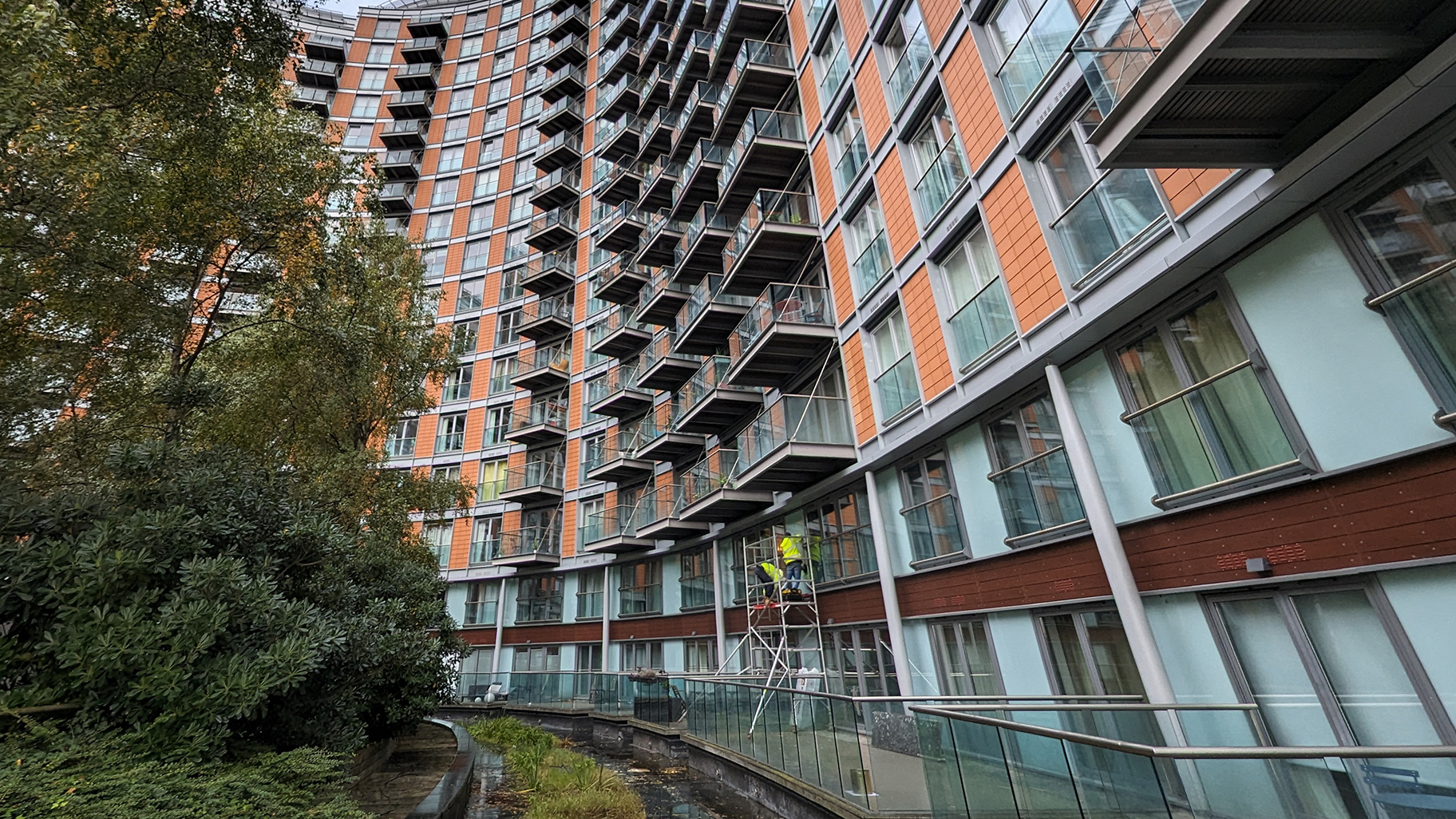
The tragic events at Grenfell Tower were primarily attributed to the composite panels with a polythene core used for cladding the building. The specific cladding material played a pivotal role in the rapid spread of the fire, bringing significant attention to the importance of recladding projects. This underscores the crucial need to rigorously adhere to safety protocols in any recladding construction endeavour. It is estimated that there are still numerous buildings, both in the public and private sectors, where extensive efforts are required to remove and replace non-compliant cladding, emphasising the urgency of addressing this issue.
Following these events, we have established a dedicated team of specialists exclusively focused on the recladding of non-compliant buildings. Leveraging our extensive in-house expertise, we oversee every aspect of the recladding project lifecycle, ensuring meticulous management from inception through to completion. Whether serving as principal contractor or subcontractor, our cladding remediation solutions are meticulously crafted to prioritise compliance, uphold superior quality standards and effectively manage costs. We are committed to prioritising safety above all else, demonstrating unwavering dedication and passion for facade remediation, thereby bolstering public confidence in the safety and integrity of the UK’s construction industry.
MAINTENANCE
Who we cater to
Our maintenance services are exclusively tailored for companies and developers. We specialise in delivering comprehensive maintenance solutions that meet the unique needs of businesses and developers. From routine upkeep to specialised repairs and upgrades, our services ensure optimal functionality and longevity of your facilities. We prioritise efficiency, reliability and professionalism in every aspect of our maintenance operations, supporting our clients in enhancing property value and operational efficiency.
Cost Savings
Regular maintenance provides significant cost savings compared to sporadic repairs for several reasons:
Preventive Maintenance
Scheduled inspections and maintenance catch potential issues early, preventing them from becoming costly problems. For example, replacing worn-out components in HVAC systems before they fail prevents expensive repairs or replacements.
Extended Equipment Lifespan
Well-maintained assets experience less wear and tear, leading to fewer major replacements or overhauls. This results in substantial long-term cost savings by prolonging the lifespan of equipment and facilities.
Reduced Emergency Costs
Proactive maintenance lowers the risk of unexpected breakdowns or emergencies. By addressing issues preemptively, businesses avoid costly downtime and emergency repair expenses that can disrupt operations.
Energy Efficiency
Properly maintained equipment operates more efficiently, consuming less energy and reducing utility costs. For instance, tuned HVAC systems use less energy for heating or cooling, resulting in lower utility bills over time.
Preservation of Property Value
Regular upkeep maintains the aesthetic appeal and functionality of buildings, preserving their market value. This enhances property investment returns by attracting tenants or buyers who value well-maintained facilities.
Compliance and Safety
Regular maintenance ensures buildings meet safety and regulatory standards, preventing fines and penalties for non-compliance. This commitment to safety not only saves costs but also provides a secure environment for occupants and employees.
In summary, investing in regular maintenance programmes is a proactive strategy that minimises operational disruptions, emergency costs and regulatory risks. It preserves asset value, improves energy efficiency and enhances overall operational efficiency and sustainability for businesses and property owners alike.
Info on PPM and reactive works/contracts
PPM (Planned Preventative Maintenance) and reactive works/contracts are integral parts of maintenance management in various industries, particularly in facilities management and building maintenance. Here’s a breakdown of each:
Planned Preventative Maintenance (PPM)
PPM involves scheduled inspections, maintenance and repair activities aimed at preventing equipment or facility failures before they occur. Key aspects include:
Scheduled Inspections
Regularly planned inspections of equipment, systems and facilities to identify potential issues early.
Routine Maintenance Tasks
Scheduled tasks such as lubrication, cleaning and calibration to maintain optimal performance.
Predictive Maintenance
Use of data and analytics to predict equipment failure and schedule maintenance accordingly.
Compliance and Safety Checks
Ensuring equipment and systems comply with regulatory standards and are safe for operation.
Documentation and Reporting
Keeping detailed records of maintenance activities, inspections and compliance checks.
Reactive Works/Contracts
Reactive maintenance involves responding to equipment failures, breakdowns, or unexpected issues as they arise. Key aspects include:
Emergency Response
Immediate response to equipment failures or emergencies to minimise downtime.
Repairs and Replacements
On-demand repairs or replacements of faulty equipment or systems to restore functionality.
Cost Management
Managing costs associated with emergency repairs and unplanned maintenance activities.
Work Order Management
Tracking and prioritising reactive maintenance tasks through work order systems.
Root Cause Analysis
Investigating the cause of failures to prevent recurrence and inform preventive measures.
Contracts
Contracts in maintenance management outline the terms, responsibilities and expectations between service providers (such as maintenance contractors) and clients (building owners or facility managers). Key components include:
Scope of Work
Detailed description of services to be provided, including PPM and reactive maintenance tasks.
Service Level Agreements (SLAs)
Performance metrics, response times and quality standards agreed upon between parties.
Duration and Renewal
Length of contract, renewal terms and termination clauses.
Cost and Payment Terms
Pricing structure, payment schedules and cost allocation for additional services.
Insurance and Liability
Coverage and responsibilities related to insurance, indemnification and liability in case of incidents.
Effective management of PPM and reactive works/contracts ensures optimal operational performance, compliance with safety standards and cost-effective maintenance strategies in facilities and building management.
End of Warranty Tests for Building Windows
At GSIM, we recognise the importance of ensuring that your building’s windows meet the highest standards of quality and performance before your warranty expires. Our comprehensive end of warranty tests provide a thorough inspection of all building windows, allowing you to identify and address any potential issues before the warranty period concludes.
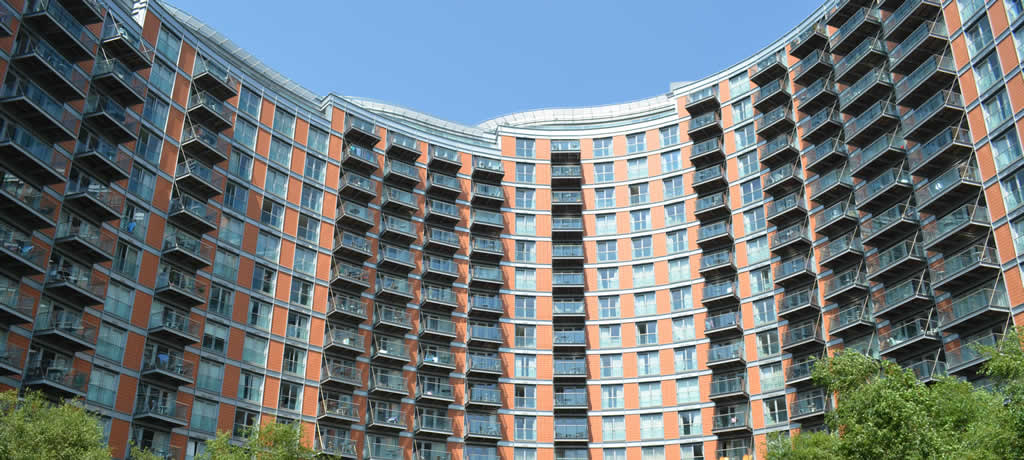
Benefits of Our End of Warranty Tests:
- Peace of mind: Our detailed assessments give you confidence that your windows are functioning optimally, protecting your investment and ensuring comfort for occupants.
- Early detection of issues: Identifying any concerns before the warranty expires allows for prompt resolutions, minimising disruption and safeguarding your warranty coverage.
- Enhanced performance: By ensuring that all components meet necessary standards, you can improve the longevity and efficiency of your windows.
- Seamless transition to PPM contracts: Upon completion of our end of warranty tests, consider transitioning to a Planned Preventive Maintenance (PPM) contract. This proactive approach ensures ongoing maintenance, extending the lifespan of your windows and reducing the risk of future problems.
- Significant long-term cost savings: Upon completion of our end-of-warranty tests, cost savings will be maximised by preventing failures, enhancing durability, reducing insurance premiums, increasing property value, and ensuring compliance with regulatory standards.